長久以來,工廠及各個生產現場始終積極實施「消除浪費」的舉措。有些人覺得這些方法顯得「吹毛求疵」,但之所以採取消除浪費的行動,主要也是為了「降低成本」。
儘管人們都很努力工作,但總是會在不知不覺間形成各種「浪費」。當每個員工都製造些許的浪費,再把時間軸拉長,一年累積下來的浪費將會十分可觀。
所以首先我們必須確認,在何種情況下會產生哪些浪費,又可能因而引發什麼樣的問題。
以下的「七種浪費」是最具代表的浪費行為:
1. 生產過剩的浪費
因為材料便宜,或是不想讓設備閒置等諸多理由,導致生產過剩。然而這勢必會形成「庫存」,衍生出倉儲費等雙重、甚至三重的浪費。
2. 等待的浪費
當工作量分配不均時,容易出現「人力閒置」的情況。所以為了防止這類情況發生,必須重新分配工作量。
3. 搬運的浪費
搬運本身不會創造價值,所以重點在於設法將搬運作業減少到零。例如,利用滾輪輸送帶或滑道(後述)輸送到下一個製程,也是解決「搬運的浪費」的方法之一。
4. 加工的浪費
在前置處理階段花時間處理不必要的細節,而且對真正加工沒有任何助益,就是一種浪費。這種情況常見於事務部門。例如,明明只是內部會議使用的資料,製作資料時卻花太多精力在排版或配色上,造成時間的浪費。
5. 庫存的浪費
有許多因素可能造成「庫存的浪費」,而且一旦出現庫存,還會另外多出庫存成本,相當於庫存總額的三成。
6. 動作的浪費
在此指的是不會產生附加價值的動作,例如,動線不良、移動時間很長,這些都算是「動作的浪費」。
7. 不良品與修正的浪費
如果出現不良品,必定會發生修正的浪費,同時失去時間、成本和信譽。如果因而發生事故,損失更加慘重。
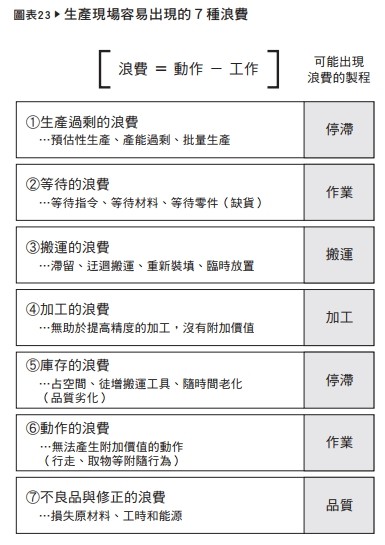
讓所有的工作都產生附加價值
用來消除這七種浪費的「消除浪費」,換個說法就是「排除不具附加價值的作業」,而且這也有益於「消除材料費、勞務費的損失」。
即使是對消除浪費最得心應手的工廠,據說每天的作業量也只有25%是「具有附加價值的『真正的』工作」,其餘的75%中,有50%是輔助事務,另外的25%僅僅是等待工作的閒置時間。到底浪費出現在什麼地方?該如何改善,才能把這75%的浪費轉換成有益的附加價值?
其實,消除「七種浪費」所追求的,是思考「如何讓工作變得具有附加價值」。
這絕非是一種「吹毛求疵」的無理要求。
作者介紹:堀切俊雄
豐田工程技術股份有限公司執行董事。畢業於九州大學工學院航空工學系,名古屋工業大學研究所修畢,產業策略碩士。1966年進入豐田汽車股份有限公司,從事日本國內生產線製程設計、設備規劃、TPS(Toyota Production System,豐田生產系統)等項目。1979年以後,足跡遍及東南亞、澳洲、紐西蘭、南非、葡萄牙、中國等海外工廠,同樣從事生產線製程設計、設備規劃、TPS。自1987年開始,參與臺灣國瑞汽車的業務管理,以及中國零組件生產業務發展規劃。
2002年成立豐田工程技術股份有限公司,擔任執行董事,協助各大公司引進TPS技術支援,客戶涵蓋日本國內企業,俄羅斯、中國、韓國等海外製造商,以及哈雷大衛森、波音等美國製造公司。
2008年設立股份有限公司豐田式管理學院,擔任執行董事,指導富士通、韓國浦項鋼鐵等企業,利用TMS(Total Management System,全方位管理系統)進行企業經營管理。2009年成立社團法人TPS檢定協會,任職理事長,致力推廣豐田模式的改善管理術。
本文經授權轉載自樂金文化《世界頂尖企業爭相效法、利潤極大化的「豐田成本管理術」:TOYOTA獲利世界第一的祕密武器》
責任編輯/郭家宏